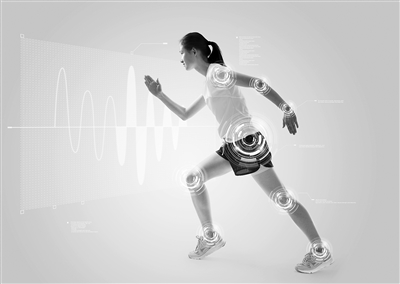
人类对热能的利用效率只有30%左右,大部分的热会以废热的形式在环境中耗散,其中2/3的废热温度低于200℃,有效回收低品位废热对可持续发展具有重要意义。
由于具有比电子热电材料高2至3个数量级的热电压,以准固态凝胶为代表的热电水凝胶等离子热电材料备受关注。
热电水凝胶材料具有哪些良好性能?未来还有哪些应用?带着这些问题,记者采访了相关专家。
一种具有优异热电性能的材料
热电水凝胶是一种具有优异热电性能的材料,被广泛应用于热电转换器件和热电散热器件等。因其具有柔性可拉伸特性,通过人为设计可制备成软硬不同、薄厚不同、颜色不同的材料,甚至可以制作成与皮肤表面共形贴合的薄膜。
太原理工大学电子信息与光学工程学院张虎林教授介绍,当把热电水凝胶材料置入有温度梯度的环境中,材料中氧化还原对的热伏效应会在材料两端形成电化学电位差。如果敷设上电极,器件两端就会产生电极电位差,即形成电压差。
热电水凝胶的制备方法多种多样,大致可以分为物理交联法和化学交联法两类,具体制备方法常见的有溶胶—凝胶法、电泳法、聚合法等。
太原理工大学硕士研究生杨航介绍,她所在的研究团队目前常用的制备方法为溶胶—凝胶法,即选择适当的溶剂,将所需的热电材料溶解其中,形成胶体溶液。在适当的条件下,通过热处理或者其他方法,将胶体溶液转化为热电水凝胶。
“聚合法也是一种化学方法,通过在单体溶液中加入交联剂、引发剂等化学试剂,使其发生自由基聚合反应从而形成热电水凝胶。而电泳法则是通过给胶体溶液通电,使其在外加电场的作用下发生聚合。”杨航说。
在日常生活中应用领域十分广泛
热电水凝胶材料在日常生活中有着很多应用案例,如热电发电机就是利用热电效应,将热能转化为电能的装置。在热电发电机中,热电水凝胶作为热电材料可以将废热转化为电能。
武汉大学刘抗研究员、胡雪蛟教授团队曾设计开发了一种智能热电水凝胶,将该水凝胶薄膜贴覆于发热元件,一方面可直接将废热回收转化为电能,另一方面,水凝胶内部的水分会快速蒸发带走热量,降低器件温度。同时,当器件停止工作后,水凝胶薄膜又会从周围的空气中吸收水分,自发实现往复利用。
与此同时,热电水凝胶还可以应用于温度传感器中,用于测量温度。由于热电水凝胶的热电性能与温度密切相关,因此可以通过测量热电水凝胶的电压差来确定温度的变化。这种基于热电水凝胶的温度传感器具有响应速度快、精度高等优点。
结合热电水凝胶的特性,张虎林团队探索的利用热电水凝胶实现无源可穿戴运动监测,也是热电水凝胶具有前景的应用方向之一。
该团队研发的柔性可食用水凝胶敏感单元,可以用来监测婴儿身体表面的生物压力。“我们将传感器附着在婴儿衣物以及皮肤上,11个压强传感器分别覆盖在胸部、手、膝盖、脚、颈部、背部、手腕和臀部等重点部位。我们预先收集了特定运动模式的信号,例如翻身、抱婴儿、拍背和鼓掌,并基于这些信号特征开发深度学习算法,可以快速准确识别婴儿的活动状态。”张虎林介绍。
尽管国内关于无源可穿戴运动监测研究还相对较少,但热电水凝胶材料可以直接贴合于皮肤或衣物,敏感单元可大可小,为无源可穿戴运动监测提供了无限可能。
南开大学马儒军教授课题组就曾设计了一种基于拉伸诱导结晶和热电化学效应的高热电性能的强韧可拉伸热电水凝胶,该项研究克服了传统准固态热电池力学强度低的限制,同时优化了热电性能,为设计具备高效热电转换以及灵活可靠的可穿戴电子设备提供了可行方案。
谈及热电水凝胶材料的发展,张虎林表示信心满满。“未来我们将立足于现有的研究成果,结合自身专业特长,不断提升信号转换稳定性,开发更适合的信号处理算法,发展一系列无源智能可穿戴器件。相信实现产业化就在不久的将来。”张虎林说。
链接
新型凝胶可实现光、热、电的转换
日前,太原理工大学电子信息与光学工程学院张虎林教授团队制备了一种光驱动柔性热电水凝胶,凝胶部分由聚乙烯醇、聚二甲基硅氧烷聚合物网络与二价铁离子/三价铁离子氧化还原对组成。该成果发表在《化学工程学报》上。
团队人员在传统热电水凝胶材料的基础上,制备了一种光驱动柔性热电水凝胶贴片。该成果采用了双层结构,上面一层由聚二甲基硅氧烷聚合物组成,并掺入二氧化硅包覆的金纳米颗粒,利用局域表面等离子体共振效应实现光热转换。下层为聚乙烯醇网络与二价铁离子/三价铁离子氧化还原对组成的薄膜,并掺入聚二甲基硅氧烷聚合物颗粒来降低热导率。“可见光的波长大概为400纳米到800纳米,当聚二甲基硅氧烷聚合物网络中的金纳米颗粒表面电子整体振动频率与可见光大致匹配,可以和可见光之间发生共振并吸收光子能量,实现光到热的转换。”张虎林解释。
张虎林介绍,热电水凝胶材料除有机框架之外,70%以上都由水组成。在北方等地区,因为干燥的气候条件很容易使热电水凝胶材料失水,从而影响其热电转化效率。
“保证水分不流失,是提升热电水凝胶性能稳定性的关键。”张虎林表示,目前国内从事热电水凝胶材料研究的团队相对较少,可借鉴经验相对不足。在这项研究中,团队历经几个月的摸索,通过调整材料内在物理化学结构,以及在外部封装防止水分蒸发两种方式,降低了材料的失水率。